QodeNext's Validation software is a powerful inline data and product validator tool for the high speed continuous online validation processes. It connects with vission systems, scanners weighing scales, PLCs, rejection systems, etc to assure qualitative output and reduces the manual QC processes required.
of components at each stage and the final inspection of finished goods to facilitate accurate production. It allows you to monitor the manufacturing tages at high speeds, trigger corrective or abortive actions to confirm the production output reliability of a determined standard.
Challenges
With high risks associated with recalls of incorrectly labelled products, faulty and substandard products, it is imperative that companies adopt validation methods to ensure final product outputs remain within specified target quality limits.
- Time taken in manual QC process
- Manpower intensive
- Loss of production throughput
- Low accuracy of manual processes
- High regulatory actions in case of inaccurate product markings
- Invalid or faulty components going into production due to manual validation
- Huge batch recalls due to substandard products or faulty finished being sent into market
- Lack of automated validation and rejection mechanism, making the process time consuming & tedious
Solution
Real-time accuracy of reading and online validation at ultra high speeds- Critical Process Parameters & Quality Attributes: Define essential operational parameters and physical attributes for desired product output within specified quality target guidelines
- Presence Absence Check: Validate the correct component by scanning the barcode against the desired component
- OCR/ OCV data validation: Validate the correct component and detection of fault component by using vision cameras to optically analyse the image
- Weighing Scale Validation: Validate correct configuration of component or final product by using a weighing scale to compare against specific weight
- Trigger Alert: Deviations from defined parameters flags an alert to take corrective action
- Rejection based on rules: If the validation based on barcode, OCR/ OCV or weight fails, the component is rejected on PLC using rejection arm
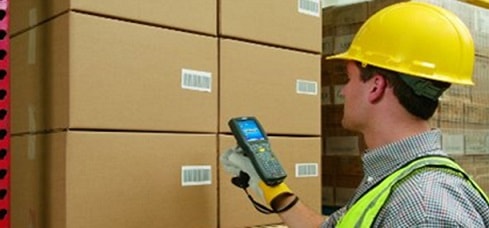
Features
The comprehensive solution facilitates the following processes- One Click Setup
- Dynamic Validation
- Rejection Trigger
- Multiple Equipment control
- ERP Integration
- Integration with robotics
Implementation
Solution
The modular and hardware independent structure makes it seamless to implement.
Software
The software can be hosted locally in the facility, at a remote data center or on the Cloud.
Technology
- Barcode
Hardware
Handheld Scanner/
Mobile ComputerVision Systems,
ScannerPLC
Rejection
Mechanism
Universal
QodeNext solutions run on most of the global leading hardware devices. We partner with global hardware manufacturers like Zebra, Cognex, Sato, Datalogic to create an open technology platform to allow you maximise your existing infrastructure.
Book an appointment with our specialists today to implement the best solution for your business requirements.
Impact
Ensure accuracy of your production and packaging environmentWith QodeNext you will be able to:
- Detect incorrect components
- Reject defective parts or finished goods
- Maintain accurate and time efficient quality checks
- Reduce manual and human intervention